Just-In-Time Inventory Management: The Ultimate Guide
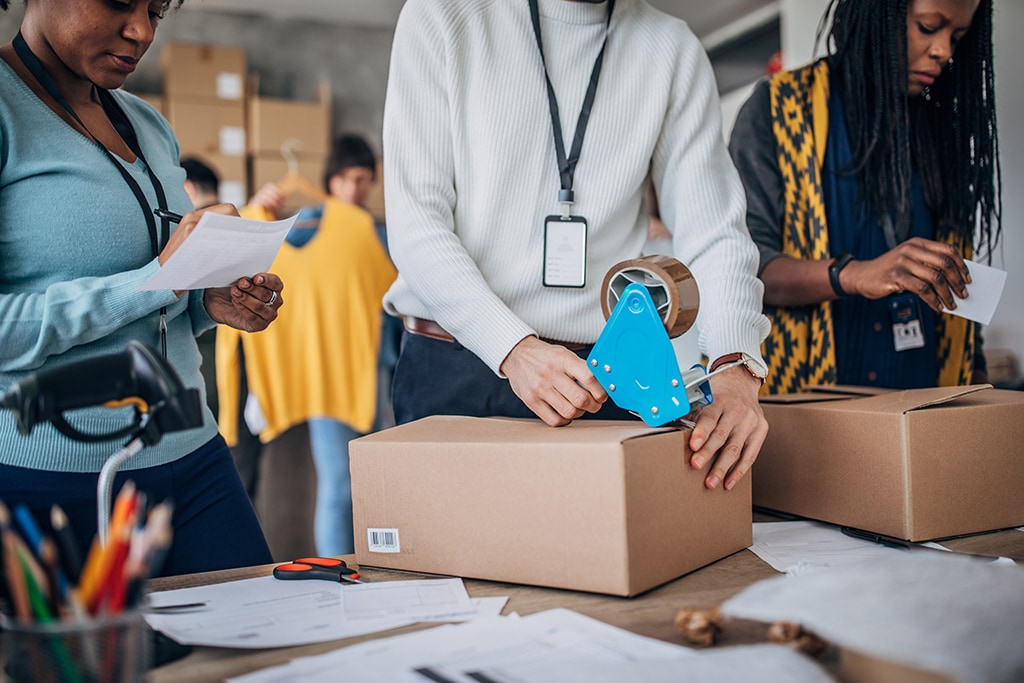
Any eCommerce business that scales beyond just selling one or two products a week must have a streamlined and efficient inventory management system.
You simply won’t survive without it.
Just-In-Time (JIT) inventory management is a popular and proven system for many growing eCommerce businesses.
In this post, you’ll learn:
- What JIT inventory management is and why it’s valuable
- Whether or not your business is a suitable candidate for JIT inventory management
- How to implement JIT inventory management in your business
- Advanced JIT concepts
What is Just-in-Time Inventory Management?
Just-in-time inventory management (JIT) is a system where inventory is only ordered and delivered on an as-needed basis.
This reduces the amount of warehouse space needed to store inventory, as well as the cost of carrying excess inventory.
The balancing act of JIT is to receive new stock right when it’s needed — if you get it any sooner than it’s needed, you have excess inventory levels and money tied up. On the other hand, if you get it too late, you might face stock-outs.
In other words, the main objective of the JIT methodology is to decrease inventory holding costs while increasing inventory turnover.
As you can probably guess, there is a layer of risk with just-in-time inventory management that requires skilled workers, advanced factory layouts, proper equipment, and sophisticated software systems to make things come together.
Why use JIT Inventory Management?
There are many reasons why businesses choose to implement JIT inventory management. The most common reasons include the following:
- Reduced inventory carrying costs: Carrying excess inventory can tie up a lot of working capital that could be better used elsewhere in the business. JIT inventory management can help reduce these carrying costs by reducing the amount of inventory that needs storing.
- Improved cash flow: Having excess inventory on hand can tie up a lot of cash that you could use for other purposes. JIT inventory management can help improve cash flow by reducing the amount of inventory that needs payment upfront.
- Reduced production costs: Overproduction is a common problem in businesses that don’t use JIT inventory management. By only producing items when there is customer demand, businesses can reduce the cost of production.
- Improved customer satisfaction: JIT inventory management can help improve customer satisfaction by ensuring that products are always available when you need them. This is especially important for businesses that produce perishable goods or goods with a short shelf life.
- Eliminated waste: The system also eliminates the waste associated with overproduction, as items are only produced when there is customer demand.
How Does Just-in-Time Inventory Management Work?
When JIT works, it’s a well-oiled machine that marches to TAKT time, which is a lean term for the rate at which customer demand is created.
To make JIT inventory management work, businesses need to have a TAKT time that’s equal to or less than the manufacturing lead time.
This means that the time it takes to receive raw materials, produce the product, and ship it to the customer needs to be equal to or less than the customer’s demand.
For this to work, businesses must have a very efficient and streamlined manufacturing process. It also requires businesses to have a razor-sharp understanding of the lead times associated with each step in the logistics pipeline.
JIT inventory management also requires good communication between the different parts of the supply chain. This includes communication between suppliers, manufacturers, and customers.
For example, if a customer places an order for a product, the manufacturer needs to be able to communicate this information to the supplier so that the raw materials can be shipped promptly.
As mentioned, the goal of JIT inventory management is to have a continuous flow of materials and products through the manufacturing process so that there is no need (or little need) for inventory storage.
This can be a challenge to achieve, but businesses that are successful in implementing JIT inventory management can reap many benefits.
Key Features of JIT Inventory Management
There are several key features of JIT inventory management that businesses need to be aware of. These include:
Inventory forecasting
JIT inventory management relies on information about customer demand to forecast when new inventory will be needed.
This forecasting can be done using various methods, such as historical sales data, trend analysis, or even market research.
Inventory alerts
Another key feature of JIT inventory management is the use of inventory alerts. These alerts can be set up to notify the appropriate personnel when inventory levels are low and new inventory needs to be ordered.
This ensures that new inventory arrives on time so that production can continue without interruption.
For example, SkuVault allows administrators to set reorder alerts for particular SKUs. That way, you don’t need to crunch these numbers in a spreadsheet (or worry that you’ll stock out).
Barcode & tag systems
Barcode and tag systems are often used in conjunction with JIT inventory management. These systems help to track inventory levels and can be used to trigger inventory alerts.Inventory security & backups
Another important feature of JIT inventory management is the need for security and backups. This is because JIT inventory management relies on having a continuous flow of materials and products.
If there is an interruption in this flow, it can cause significant problems for the business. That’s why businesses need to have security measures in place to protect their inventory and safety stock in case of problems.
History of Just-in-Time Inventory Management
Just-in-Time inventory management is a part of lean manufacturing, a methodology that originated in Japanese manufacturing facilities.
JIT was first developed and optimized within the Toyota manufacturing plants by Japanese industrial engineer and businessman Taiichi Ohno.
It came about as a way of meeting customer demands with minimum delays. It is commonly referred to as the Toyota Production System or TPS.
In fact, JIT is what TPS is called now, and it has been credited with helping Toyota become one of the most successful automakers in the world.
We can’t mention the Toyota Production System and lean manufacturing method without also mentioning industrial engineer and statistician W. Edwards Deming. He was one of the first management consultants to work with Toyota in the 1950s and was instrumental in its success.
The lean business methodology is all about continual testing and iteration, and JIT is the pinnacle of lean thinking.
JIT is a practical application of lean manufacturing that removes all waste from the production process, so businesses can produce only what is needed when it is needed and in the quantity that is needed.
This results in a significant reduction in inventory levels and lead times, as well as an increase in overall efficiency. JIT has been adopted by many businesses around the world and is considered to be a best practice in manufacturing.
Advantages of JIT Inventory Management
We’ve already reviewed many of the benefits of JIT, but business.org summarizes them quite nicely:
“When implemented correctly, a JIT inventory system can help retailers and lean manufacturing businesses reduce their storage costs and keep their inventory fresh. Of course, JIT inventory systems fall apart without prompt, reliable item production and shipping. But once you get it down, JIT systems can enhance the efficiency and profitability of your business.”Disadvantages of Just-in-Time Inventory Techniques
Despite the advantages, there are some disadvantages to consider before implementing a JIT inventory system in your business.
First, JIT requires a high level of coordination and communication between all members of the supply chain — from suppliers to manufacturers to retailers.
This can be difficult to achieve and maintain, especially if you have a long supply chain or if your suppliers are located in different parts of the world.
Smaller eCommerce businesses often don’t yet have reliable supplier relationships. This lack of a trustworthy infrastructure may preclude them from using JIT in their early stages.
Second, JIT systems can be disrupted by external factors beyond your control, such as bad weather, strikes, natural disasters, or — you guessed it — global pandemics.
Covid’s disruption of the microchip manufacturing pipeline is just now starting to rebound (two years later).
Third, JIT inventory systems require a high level of investment in technology and infrastructure, such as ERP systems, inventory management systems, RFID tags, and real-time data analytics. This can be costly and may not be feasible for all businesses.
Finally, JIT inventory systems can be difficult to implement and maintain and require a high level of commitment from all organization members.
If you’re considering implementing a JIT inventory system in your business, weigh the advantages and disadvantages carefully to decide if it’s the right fit for you.
Risks of Just-in-Time Inventory Management
JIT inventory systems can definitely be a “high risk, high reward” methodology. The most significant risks include the following:
- Inventory shortages: A JIT system depends on a continuous flow of inventory to maintain production levels. If there are any disruptions in the supply chain, it can lead to inventory shortages and production delays.
- Increased costs: JIT systems require a high level of investment in technology and infrastructure. This can be costly and may not be feasible for all businesses.
- Implementation difficulties: JIT systems can be difficult to implement and maintain and require a high level of commitment from all members of the organization.
Who Should Use a JIT System?
A JIT system is best suited for businesses that have a high level of coordination and communication between all members of the supply chain.
As discussed, JIT systems require a commitment to detail and organization from all organization members, meaning it’s important to ensure everyone is on board before attempting implementation.
JIT systems are also best suited for enterprises with a high level of investment in technology and infrastructure.
This includes businesses with robust MRP and ERP systems, Inventory Management Systems, RFID tags, and real-time data analytics.
Managers and executives implementing a JIT system should also be fully educated in the principles of lean manufacturing, Six Sigma, and JIT to avoid the many risks and pitfalls associated with its implementation.
If you want to have a lean enterprise, it’s a good idea to start by reading Lean Thinking: Banish Waste and Create Wealth in Your Corporation by James Womack.
Consider these questions as a framework to guide you in the decision-making process:
- Do I operate with very predictable and measurable manufacturing lead times?
- Do I leverage inventory management software to forecast demand?
- Can I maintain safety stock in the case of a logistics interruption?
- Do I have a team that sees the value in the lean business methodology (or at least, can they be persuaded)?
If you answered yes to most of these questions, you’re likely a prime candidate for the JIT methodology.
How Can I Make My JIT System Work for Me?
By following these four steps, you can make JIT work for you and your organization:
- Eliminate waste: The first step is eliminating all forms of waste in your organization. This includes overproduction, waiting, transportation, motion, defects, and inventory.
- Identify and correct problems: Once you’ve eliminated waste, you must identify and correct any problems that could lead to production delays or disruptions. This includes problems with suppliers, equipment, and the production process itself.
- Ensure your logistics pipeline is efficient. An “efficiency audit” includes ensuring that your machines are properly maintained and that your production line is set up in the most efficient way possible. You should also track your inventory levels closely and monitor your production process to identify any bottlenecks or areas of improvement.
- Maintain robust quality assurance. Effective traceability methods with root cause analysis, problem cause correction, follow up and continuous improvement are critical for ensuring a smooth JIT production process.
- Select the proper equipment (and software). When choosing equipment and software for your JIT system, it’s important to select tools that are reliable and have a low rate of defects. This is where Six Sigma troubleshooting and data analysis comes into play. You should also consider the maintenance requirements of the equipment and the overall cost of ownership.
- Train your employees. Proper training is essential for ensuring that your employees can effectively operate in a JIT environment. Employees should be properly trained on the principles of JIT and lean, and they should also be familiar with the specific processes and procedures associated with your organization’s
- Secure your factory’s supply chain. To maintain a continuous flow of inventory, it’s important to have a secure and reliable supply chain. You can accomplish this by developing strong relationships with your suppliers and working to ensure that they can meet your demand.
JIT Inventory Examples
Automotive manufacturers, who often measure TAKT time down to the minutiae, are prime examples of businesses successfully implementing JIT systems.
To maintain a continuous flow of inventory, automakers rely on suppliers located near their plants. This allows them to receive parts and components quickly and minimizes the risk of production disruptions.
One notable example of a business that uses JIT in its processes in the United States is the Hyundai plant in Montgomery, AL. The plant manufactures vehicles like the Elantra sedan and the Santa Fe and Tucson SUVs. To ensure a smooth and efficient production process, the plant uses a just-in-time inventory system.
This system allows the plant to receive parts and components quickly and minimizes the risk of production disruptions. Everything from temperature control to advanced robotics is managed by engineers who are all geared toward keeping the line flowing and reducing waste.
Final thoughts
There is no perfect inventory management methodology. Each has its downsides, risks, and potential rewards. JIT is one of the most challenging yet potentially lucrative forms of inventory management.
It can drastically reduce your inventory storage costs and eliminate all waste from your organization. At the same time, businesses without a firm hold on their lead times can run into safety stocks and, thus, unhappy customers.
Whatever inventory management path you choose, there’s one thing that’s for sure: trying to stay on top of your logistics pipeline with spreadsheets (or, worse, in your head) is a fool’s errand.
You need a tool like SkuVault to automate reorder alerts, track all your lead times, and forecast buyer demand.
Thankfully, SkuVault’s inventory management software does all this and much more. To see it in action, sign up for a demo via the link on this page.
[html_blocks id=”20106″]