First In First Out (FIFO) inventory method Is now supported within Linnworks
Following the release of our Expiration Date and Batch Tracking functionality, you will now be able to utilize the First In First Out (FIFO) inventory method within Linnworks. This specifically enables you to reduce the risk of product spoilage, while improving the practice of stock valuation.
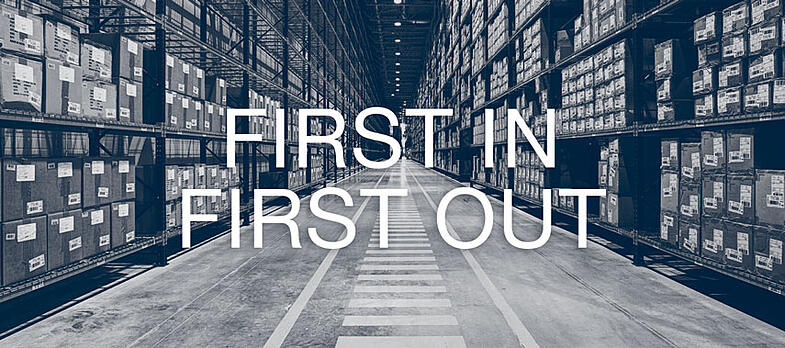
What is First In First Out?
First In First Out is a supply chain best practice that refers to the sequence in which new inventory is booked in and subsequently dispatched. Within Linnworks, you can assign either an expiry date or a priority value to your inventory items, which will define the order in which your inventory is dispatched.
While the operational use of FIFO is important for reducing obsolete inventory, First In First Out is also a method of inventory valuation, with many companies operating this method irrespective of the actual flow of goods.
As an online seller, it is integral that you are valuing your inventory accurately, for the simple reason that it can simplify your financial analysis and allow you to better track your profit margins.
With the price of inventory increasing over time, there is a strong chance that the price you pay for one batch of products will differ from the price you pay for a batch of the same product at a later date. By using FIFO, you can more accurately align the inventory cost to current market value, which in turn provides a better representation of inventory value and replacement costs. Within Linnworks, this works by assigning the inventory costs of the stock that is due to expire the soonest, or has the most imminent priority value, to the most recent sales.
The benefits of using FIFO.
First In First Out remains the most widely used inventory management method, providing retailers with various benefits. These include:
Reduced Product Wastage.
By dispatching your oldest stock first, you reduce the risk of your inventory becoming obsolete. While this method is more commonly used for items with shorter shelf lives, i.e. food and beverage, it is worth keeping in mind that the longer an item of any kind is in storage, the more likely it is that the packaging will become damaged or tarnished. By using FIFO, you minimize the chances of this happening altogether.
Reduced Impact of Inflation.
While inflation is a risk for all businesses, as your newest stock is sold last when using FIFO, it is easier to match your inventory costs to this inflation. In other words, your most recently acquired stock can be sold at a price that better reflects current market value, helping you minimize the worst effects of inflation.
Higher Gross Profit.
Assuming the cost of inventory is rising, FIFO will ensure that the older inventory cost is applied to the cost of goods sold. This specifically results in a lower expense on your income statement and a higher profit. This in itself provides a more accurate representation of your business’s profitability.
Using FIFO within Linnworks.
The introduction of our new inventory batch tracking and multiple bin locations functionality means that FIFO is now supported within the Linnworks system. If you are wanting to operationally utilise the First In First Out method, we would recommend that you follow the practice of stocking based on batch numbers.
While you will be able to use FIFO to determine the value of your stock, keep in mind that for unbatched items, Linnworks will continue to use the mean average of all quantities you have available in the warehouse. You can learn more about how both stock valuation examples work in our documentation.
Ultimately, without an advanced inventory management solution, it is incredibly difficult to identify when an item was purchased and by whom. The ability to use FIFO within Linnworks is only a small part of our newly released inventory management functionality, and we now enable complete inventory batch tracking, as well as expiry date tracking and the ability to split inventory across multiple bins in the same warehouse.
We would recommend watching the video below to learn more about our inventory batch tracking.