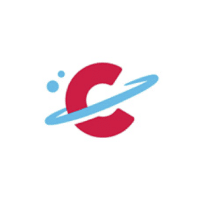
How Tootonic experienced significant growth using Linnworks automated inventory and warehouse management
New commerce connects
Find out how Linnworks can help grow your business.
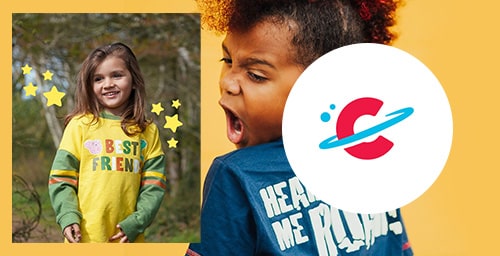
Character, the trading name of Tootonic Limited, is a UK-based online retailer that puts smiles on faces with clothing that’s fun to wear, easy on the wallet and kind to the planet.
Character was founded by parents and created on the premise that everyone loves character clothing, even big kids who should know better. Founded in 2009, they provide the latest trends, best value and biggest choice for character clothing, nightwear and accessories. Character understands the importance of kids wanting to look “cool,” which is why they take care to source the styles kids want to be seen in, at a price that won’t break the bank.
Challenges: Lack of control over stock due to manual processes
Today, Tootonic is a £53 million company. The company has grown at a fast pace over the past decade and a half.
Growth came with its challenges. Emma Hewitt, General Manager at Tootonic, explained that inventory management processes were manual in the beginning.
She said, “We were working from spreadsheets, but as we grew as a company, we realized we needed software to help manage our stock.”
And this is how the partnership between Tootonic and Linnworks started.
In 2011, two years after its founding, the team at Tootonic began using Linnworks as a solution for automated inventory management. Initially, the main use of Linnworks was to control stock levels.
Then, over time, as both Linnworks and Tootonic grew, they expanded together.
“At first, it was just a case of using Linnworks to control stock levels everywhere,” Emma said. “Over the years, we started to use all the Linnworks functionality and we’ve grown our company along with Linnworks.”
Tootonic was using the core Linnworks inventory and order management automation features, but as the business continued to expand in the last few years and became more complex with growing product ranges, Emma and the team quickly realized that they needed a solution to manage warehouse operations.
“We were working from pieces of paper in the warehouse and grew to a size where it wasn’t sustainable anymore. We came to a point where we started to lose more stock and found it very difficult to know where stock was located.”
In the earlier days, Tootonic had a small team who knew exactly what they were doing and how the warehouse operated. But as the company grew, they were hiring temporary staff. They no longer had a small staff team, so they needed a system that would make picking and packing jobs easier for their employees and one that could easily onboard new team members.
“Employees were writing things down on paper and in spreadsheets on where the stock was located and customer orders were getting all mixed up,” Emma shared “It got to a crunch point of us being too big as a company to carry on this way. We needed to know where all stock was and we needed to move away from printing out bits of paper every morning.”
Solution: An all-in-one inventory and warehouse management platform
Emma and the team were delighted when Linnworks introduced the beta version of their warehouse management module in 2019. Emma saw the value of managing inventory and warehouse processes all from one platform.
“If you’re a current Linnworks user, it is so much easier to use Linnworks warehouse management than an external one,” Emma said. “If you try to integrate an external system, there will be areas that don’t quite work as they’ve been built differently.”
Linnworks warehouse management is an extension of the platform’s core functionality, making it familiar and easy to use for existing Linnworks customers.
Tootonic was one of the first customers to use the Linnworks warehouse management module as part of the beta testing process and they’ve been instrumental in its evolution with their invaluable feedback.
“I like to think in some areas we’ve had input in the way Linnworks has evolved,” Emma said.
Initially, changing the way they operate as a business was daunting for Tootonic as they’ve always been a company that follows the principle, “If it’s not broken, don’t try to fix it.”
But they could see the long term impact Linnworks warehouse management was going to have on the business. Emma felt comfortable and confident that the Linnworks team would be there to provide support.
“I’ve always loved the support side of Linnworks,” Emma shared. “Whenever we’ve had any issues, it’s always been very easy to reach out and get somebody to help.”
Results: Automated and efficient warehouse operations running seamlessly
Emma admitted it took time for the team to get up to speed and embrace the change as the automated warehouse management system was completely new to all of them, but “now, if somebody starts on a temporary basis, it’s very easy and simple to teach them.”
Ultimately, Linnworks warehouse management has had a positive impact on operations.
“With Linnworks warehouse management, it’s much easier to locate all our stock and we’ve been able to fully automate processes including dispatch,” Emma said. “We’ve saved time and sped up processes that were previously done manually.”
Emma has noticed the difference in efficiency as well “Linnworks warehouse management has made our business much more efficient, and in particular on the stock side of things. It’s helped enormously.”
Simon Ball, Operations Director at Tootonic, has been with Tootonic for the last year. Reporting is key for him in his role.
“We’re able to pull the data for picking and packing and use it for our overall reporting numbers, which has been very helpful,” he said. “We’ve also been able to manage the stock and operations of more than one location because of the Linnworks warehouse management module.”
“A warehouse management system is invaluable”.
With a combined wealth of online retail experience and expertise, Emma and Simon know what to look out for when investing in a warehouse management solution.
Simon explained the importance of choosing a system that compliments your existing infrastructure.
“Make sure you choose a warehouse management system that integrates with the other platforms you use and do your research,” he said. “Have a seamless transition between your platform, your key selling platform and what you do as a business to set you up for success.”
Learning from previous experience, Emma encourages companies to embrace change, “Don’t be daunted or scared about changing up the way you work. Unless you’re a one man band or only have 10 SKUs, a warehouse management system is invaluable and will make your life so much easier.”
Feeling confident about international expansion with Linnworks
The main future focus for Tootonic is further worldwide expansion by exploring different Amazon regions, new fashion marketplaces including Zalando and Walmart, as well as seeing what else can be done with their own website and replicating it in places like the Middle East.
Tootonic has experienced tremendous growth and feels confident that Linnworks can continue to handle the amount of orders that come through and has been the reason they can expand into new marketplaces with complete peace of mind.
Simon is keen to make the financial side of business run as smoothly as the operations side by exploring the potential accounting integrations that Linnworks provides.
Emma and Simon are excited to see future enhancements and developments made on Linnworks warehouse management to take their operations to the next level.
Download case study